Spiral pipe
Category:
Product Introduction
Surface treatment method:
1. Cleaning
Application of solvent, emulsion cleaning steel surface, in order to remove oil, grease, dust, smooth agent and similar organic matter, but it can not remove the appearance of steel rust, oxide skin, welding flux, etc., so in the production of anti-corrosion only as auxiliary measures.
2. Tool rust removal
The first use of steel wire brush and other tools to polish the appearance of steel, can remove loose or warped oxide skin, rust, welding slag, etc. Rust removal of hand tools can reach Sa2 level, and rust removal of power tools can reach Sa3. If the steel surface is attached with strong iron oxide, the result of rust removal of tools is not ideal, and the depth of anchor pattern required by anti-corrosion construction cannot be reached.
3. Pickling
General use of chemical and electrolytic two ways to do pickling disposal, pipeline anticorrosion only use chemical pickling, can remove the oxide skin, rust, old coating, sometimes can be used as a sandblasting rust after disposal. Chemical cleaning can certainly make the appearance of the inevitable cleanliness and roughness, but its anchor pattern is shallow, and easy to form pollution.
4. Rust removal by spraying (throwing)
Spraying (throwing) rust removal is driven by a high-power motor to twist the spraying (throwing) blade at a high speed, so that abrasives such as steel grit, steel shot, iron wire segments, minerals and the like can spray (throw) the appearance of the steel pipe under the effect of centrifugal force, which can not only completely eliminate rust, oxides and dirt, but also achieve the required average roughness under the effect of abrasive fierce impact and friction.
After spraying (throwing) the rust, it can not only expand the physical adsorption effect of the pipe appearance, but also strengthen the mechanical adhesion effect between the anti-corrosion layer and the pipe appearance. Therefore, spray (throwing) rust removal is an ideal method for pipeline anti-corrosion. Generally speaking, shot blasting (sand) derusting is mainly used for pipe inner and outer surface disposal, shot blasting (sand) derusting is mainly used for pipe surface disposal.
Quality Assurance
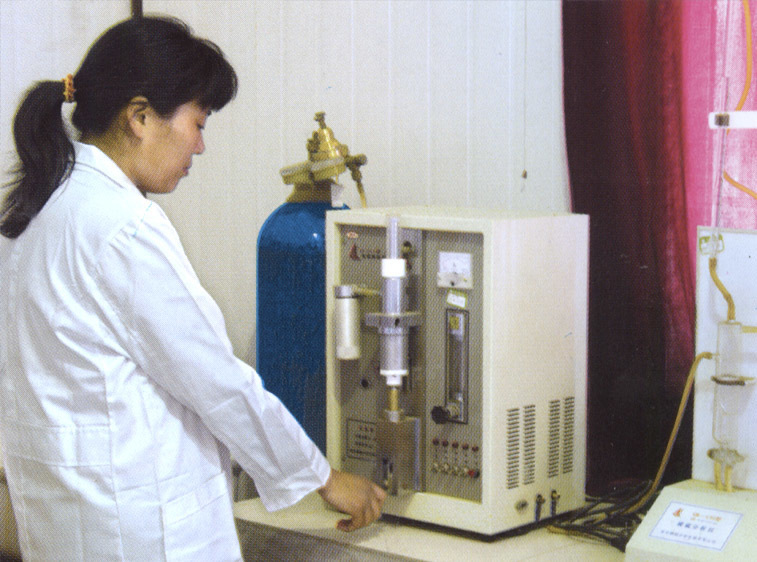
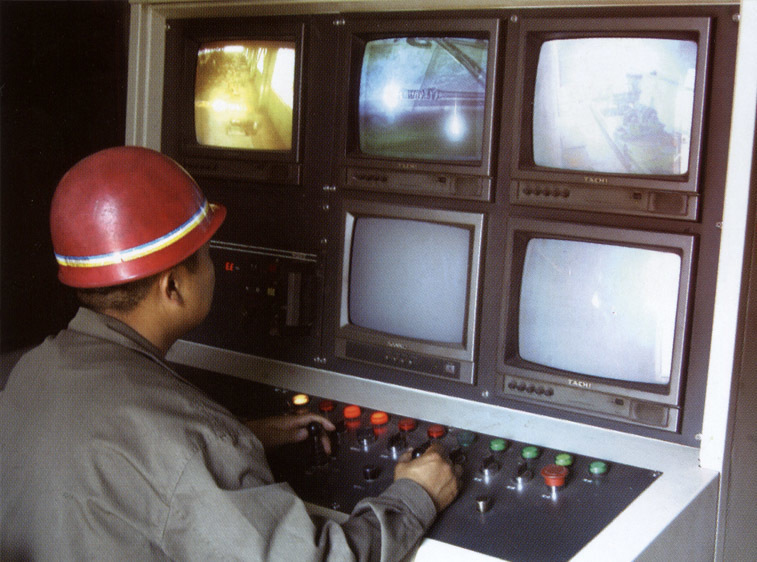
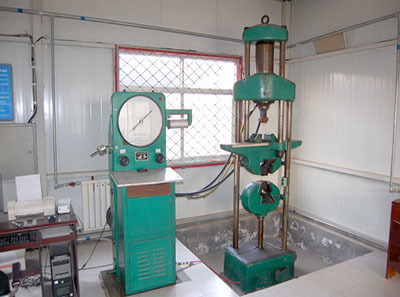
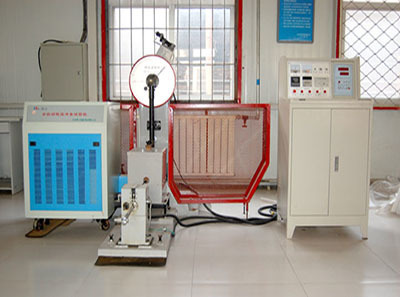
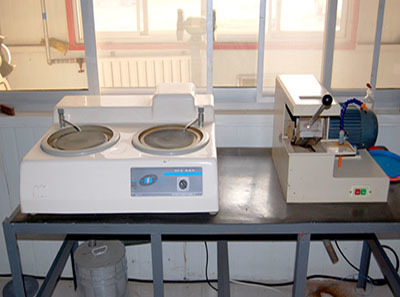
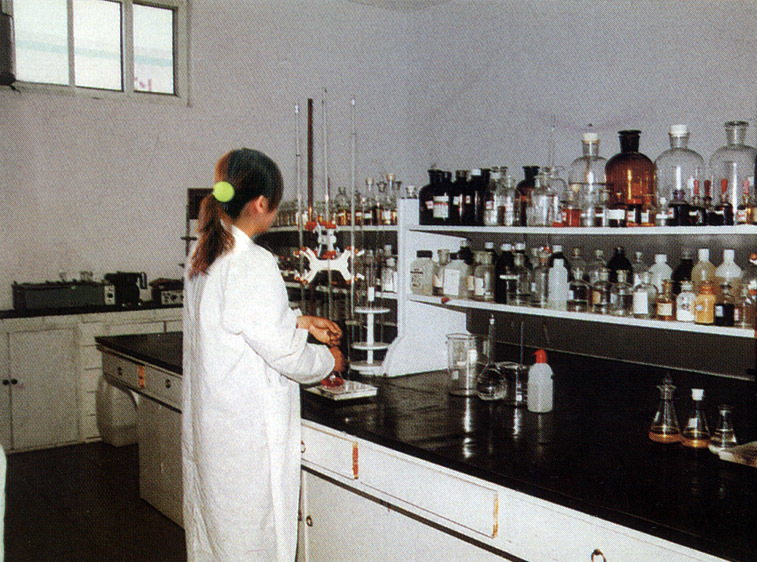
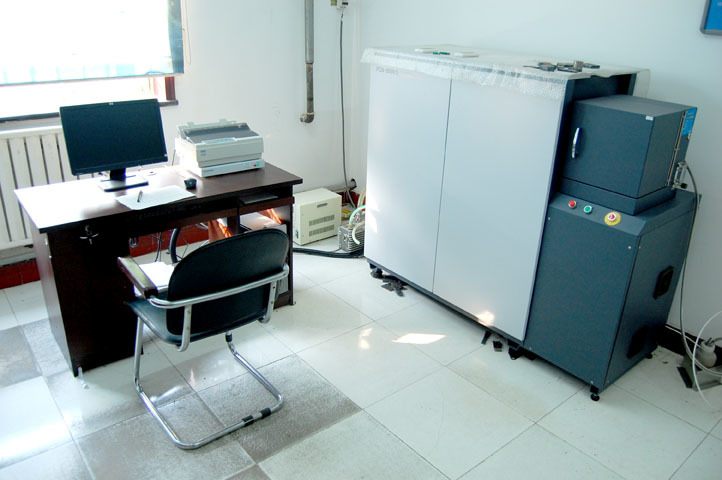

Key words:
Product Consulting
Related Products